- RaceShocks.uk
- Page
BOS Suspension Technology
THE FCV: The Frequency Control Valve :
The intelligent suspension.
This is a frequency control valve.
One of Bos’ finds is the FCV valve. A unique system, as simple as it is revolutionary, which makes it possible to detect the direction of the force exerted on the suspension. This is a small moving aluminum part that changes the hydraulic circuit depending on the direction of the excitation. If the force is coming from the bottom up, like on small bumps, the bike will feel smoother than if the force is coming from the top down, like on big compressions.
This weight is activated according to the frequency of the shock wave in order to obtain a flexible suspension on small shocks (excitation of the fork from the ground upwards, due to the holes to be erased) and strengthens on large compressions (excitement of the pilot’s fork towards the ground as when landing a jump.)
Increases comfort in the vehicle and reduces acceleration experienced by the driver. This allows you to increase the speed in the most difficult passages. Less risk of a puncture, less stress on all the mechanical parts of the chassis. Also reduces rider fatigue in the most severe impacts.
On the rally, the feedback from the drivers has been very good, with several victories at stake, such as in the Dakar stages with Carlos Sainz.
Originally developed for mountain biking: in 2013 the BOS rider won a downhill mountain bike world cup round in Andorra. It was at this time that the decision to use this technology in MX was taken.
The FCV is an answer to a problem known to pilots: the suspensions blocking on the biggest shocks. For a short time, on very big shocks the suspensions lock up. On this point all the shock absorbers behave in the same way and this has consequences on the fatigue of the pilot.
Manufacturers have always groped to find solutions, the most common temptation being to reduce the hydraulic curve, giving an impression of comfort on certain impacts.
BOS Suspension engineers took a rather different direction, focusing directly on the particularities of these strong percussions. You can’t contradict fluid mechanics, you have to adapt to it. We have therefore worked to be able to adjust and redefine specifically the threshold from which the wheel is allowed to go up during these strong impacts.
The solution is a unique frequency sensor: The weight of the FCV system is tuned to move only at high frequencies. The system only opens on strong percussion by increasing the flow through the valves.
Originally developed for mountain biking, this technology has proven itself in competition:
in 2013 the BOS rider Rém Thirion won a downhill mountain bike world cup round in Andorra with a fork equipped with FCV. It was at this time that the decision to apply this technology to MX motorcycles was taken.
In motocross, Livia Lancelot wins with the FCV-equipped air fork less than a month after its release.
In car rallying, the feedback from the drivers has been very good, with several victories at stake, such as in the Dakar stages with Carlos Sainz
Available on our: Car shock absorber, Downhill Obsys MTB fork, Downhill DH Enduro Idylle MTB fork; MTB Enduro DH All Mountain Deville II 35 FCV fork.

THE CASE: Selective Damping Control: put all the power to the ground.
Initially tested on mountain biking in 1999, it attracted attention with Nicolas Vuilloz’s victory in the world championship in 2001 and 2002, then was adapted for the Dakar Rally, won in 2005, 2006 and 2007 on BOS.
This is a principle of formidable efficiency: it corrects the hydraulics of the shock absorber according to the load applied to the wheels, thus allowing faster recovery of grip and better traction.
We used this system a lot, especially in cars from 2005 with Mitsubishi. When there is no longer any load applied, the resistance of the shock absorber corrects itself to allow the wheel to follow the terrain and regain contact with the ground. It allows better traction, grip when accelerating and braking, as it maximizes contact with the ground.
This technology is the fruit of long work on the proportioning of the loads applied to the shock absorber.
The system is closed when stopped. As soon as the applied load is lower than the stiffness of the system, the system opens.
This is equivalent to accelerating the rebound of the shock absorber after the compression phase. As soon as the contact is recovered, the normal hydraulic curve is found again.
Available on ranges
CR and XC
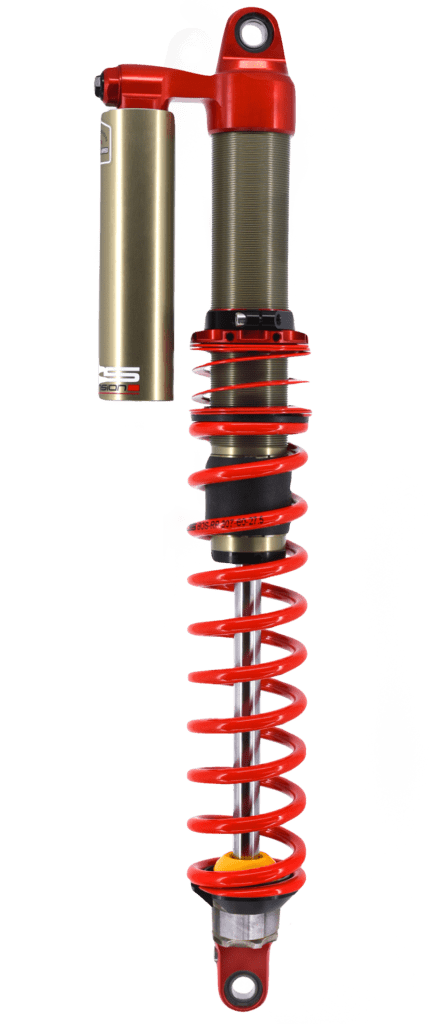
THE LOW SPEED PISTON
Initially tested on mountain biking in 1999, it attracted attention with Nicolas Vuilloz’s victory in the world championship in 2001 and 2002, then was adapted for the Dakar Rally, won in 2005, 2006 and 2007 on BOS.
The low-speed piston is a technology specially designed and developed by BOS Suspension, and particularly suitable for disciplines where the level of grip is high, such as asphalt rallying or circuit racing.
The low-speed piston is a piston specifically dedicated to controlling all “very low speed” movements, less than 250 mm/s, which are similar to all phases of setting the vehicle in motion, whether in roll, or in pitch (dive in braking, rearing in acceleration).
Unlike a traditional shock absorber, which frequently manages this zone of very low speeds simply and solely via a pressure drop calibrated by a leak, the low-speed piston, which will be mounted “in series” with the main piston, will allow to work “hydraulically” on this pressure drop, by controlling it via a piston and a dedicated valve.
We therefore have the possibility of carrying out load and stiffness variations for these speed zones so often neglected and yet oh so important in vehicle control, in the application of the load to the tires, and in the grip feedback felt. by the pilot.
This is an undeniable plus, because it gives an almost infinite possibility of adjusting the load for these low levels of shock rod speed, and therefore makes it possible to achieve much more precise and optimized hydraulic curves.
We gain this body control for all the car’s weight bearing movements, which makes all the difference.
Used for the first time on the “Factory Factory” settings of the Renault Clio S1600, this patent has since been the delight of all customers eager for high-level performance in asphalt rallies in particular.
This patent is available as standard in some models of our CR range, and can be offered as an option on request.
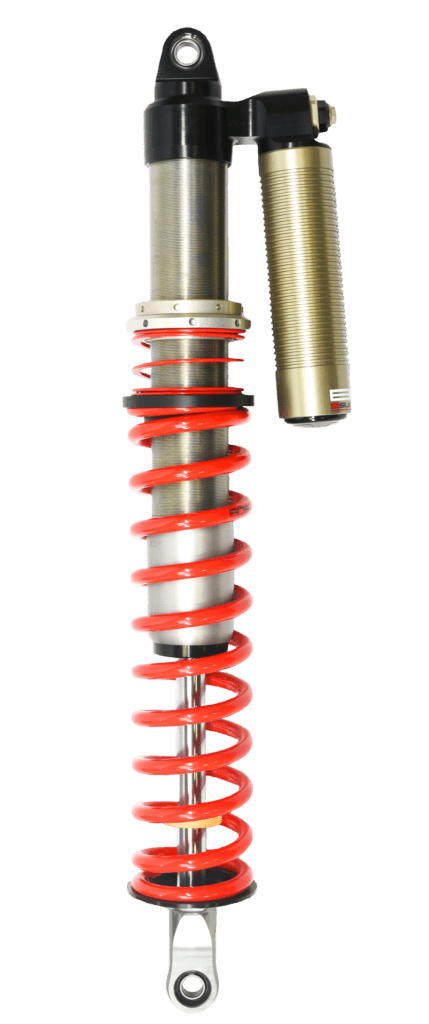
THE ADJUSTABLE HYDRAULIC STOP:
A significant plus
On the shock absorbers, the stops prevent bottoming out at the end of the stroke. But they do not prevent the feeling of the pilot when the shock sinks its full travel.
The traditional stops may well prevent heeling, when it is not progressive, it causes a shock at the end of the race. As soon as there is a little energy, it remains sensitive for the pilot.
BOS engineers have done a great job of dissipating energy on this key moment.
We have worked extensively with car manufacturers on this system. The big job was to switch the system on the bike. For us, it goes without saying to put a hydraulic stop; we have been using it since 2003 in Rally-Raid and WRC
The hydraulic stop is a system which makes it possible to harden the suspension considerably at the end of travel, in order to avoid bottoming out and improve travel management (sensation of infinite travel).
Managing this function by a hydraulic system makes it possible to vary the response according to the stress by giving it excellent progressiveness, this also avoids the violent relaxation generated by a foam pad or by a pneumatic system.
Its behavior is precisely defined during the design and allows you to ride with a softer hydraulic curve for more comfort in the middle of the travel.
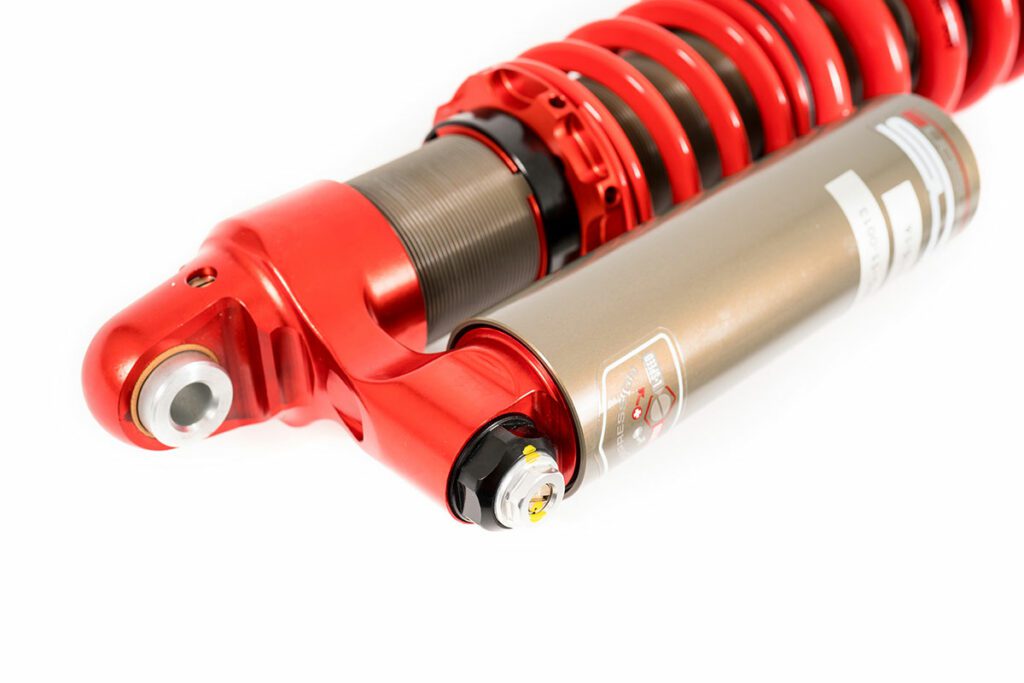